The project aimed to modernize packaging equipment and systems to enhance performance, reduce costs, and accommodate future production growth. It consisted of three parts: assessing current equipment to identify gaps and improvement opportunities, identifying future growth needs with concept designs, and valuing existing equipment for insurance and Capex planning. Completed within six months, the project addressed the client’s aging packaging infrastructure, which included high-speed can, bottle, and keg lines. With market trends shifting towards cans and specialty beverages, the client needed a plan to match future growth opportunities. First Key audited the entire packaging hall, including equipment, systems, processes, and forecasts. In Part 1, First Key assessed equipment conditions and identified improvement opportunities. Part 2 involved requirements for future growth, SKU diversity, and equipment obsolescence. Throughout the project, First Key maintained communication with the client, providing updates and collaborative solutions. Deliverables included a report on current equipment status, short and long-term recommendations with cost estimates, modernization suggestions, a conceptual future packaging hall layout and an equipment valuation was also provided. Ultimately, the project improved short-term performance, safety, quality, and established a long-term plan to reduce costs and enhance product flexibility.
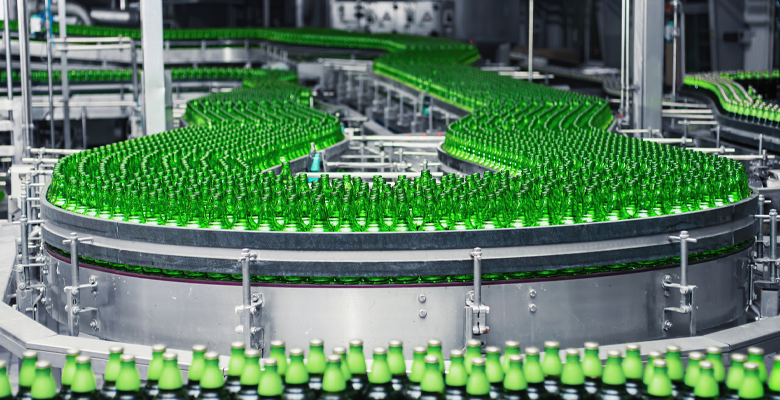